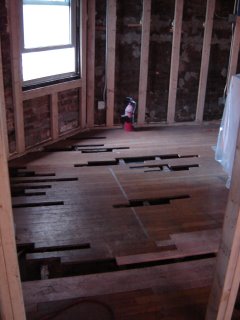
The crew has been working on repairing the existing oak and maple floors upstairs this week. They have gone through 5 bundles of oak. We had some maple left over from the 1st floor, which they used.

According to our contractor, the floors have been sanded numerous times and so this sanding will be their last. This is why it pays to take care of your wood floors and screen them when needed rather than sand them and run them down till they have to be replaced. This building was a rental for so long and took alot of abuse so this is what we've got to work with now.
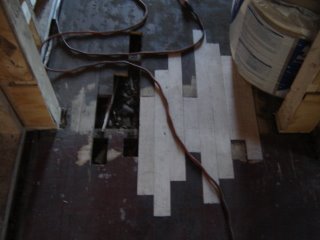
Here's a maple floor repair in progress in the kitchen and hallway. It is pretty much finished now, but Steve thinks they did not put the wood boards on sleepers and so they may have to be redone. In case you don't know what "sleepers" are... In the past, floors were raised off the subfloor by strips of wood about 1" thick by 1 1/2" wide called sleepers. It reduces noise overhead. I believe it's done now when you put radiant heat under your floor, but otherwise is not typical. I'm no expert on this though- so feel free to pipe up if you know something more.
As for our electrical inspection, the inspector asked for the following changes:
1. All 3 panels need to be on the same wall. Right now one is on an adjacent wall-it has to be moved. The only way this panel would be allowed on an adjacent wall is if there was 3 feet of clearance and we do not have room there because there is a window right next to it. This means we have to move our laundry sink and washer/dryer to accomodate this. Not major, but a job.
2. The telephone and cable lines need to have a control panel in the apt. so that the resident of the apt. has complete control and no one else can tap into it. Stealing cable or phone service is the concern I guess.
3. The junction boxes for the ceiling fans have too many pipes coming into them and so the boxes muct be larger to accomodate the wiring. We had to wire most conduit at the ceiling because our 2X4s are flat on the wall and don't allow the depth for conduit. We did this to avoif losing any footprint in the unit.
4. There must be exterior lights on each back porch that operate with a switch. We currently have electric eye lights on the 2nd floor landing.
The electricians were here until 9:15pm tonight till they couldn't see anymore. We bought them pizza. Tomorrow we'll have alot of workers here and we will be working on the wood pile- we're getting close to starting staining.
2 comments:
Sleepers were used so that the finished floor boards could be run in the same direction as the subfloor.
In most houses, the joists run side to side, but the desired finished floor is from front to back.
The subfloor had to be laid at right angles to the joists, and you can't lay the finished floor in the same direction directly on top of the subfloor.
Therefore the sleepers run at right angles to the subfloor, and the finished floor at right angles to the sleepers, i.e. parallel with the subfloor, or front to back.
Another solution to this was to run the subfloor boards diagonally. But this was more time consuming and expensive. But it made a better job.
Of course, today plywood is used as a subfloor, eliminating this problem altogether.
Sleepers actually make the floor more squeaky and louder because the boards flex between the sleepers from the weight of walking on them. The more they are sanded - becoming thinner - the more they flex and become more noisy.
wOW. We're quietly going broke waiting for the cement to get done in cicero. sigh.
Post a Comment